The distinction between socket wrench and ratchet wrench systems lies in their fundamental mechanical approaches to torque application and user interface design. A socket wrench employs a modular system where interchangeable sockets attach to a separate drive handle, creating a flexible tool configuration optimized for specific fastener requirements.
Socket Wrench System Architecture
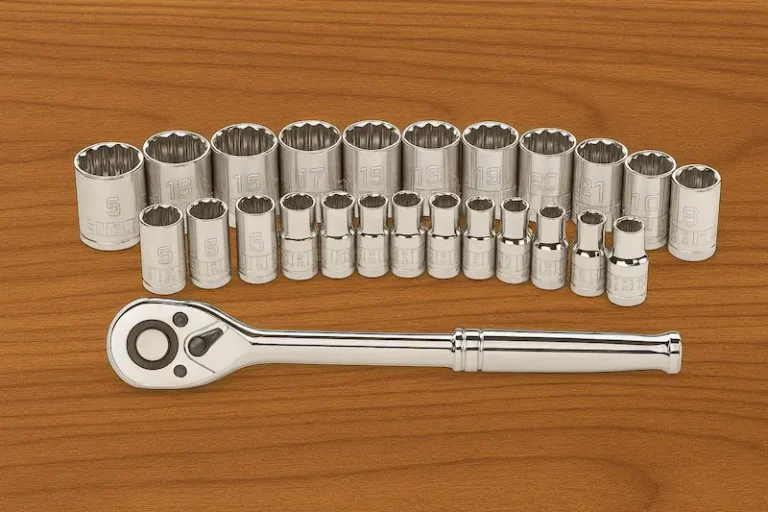
The socket wrench operates on a drive square interface standard (typically 1/4″, 3/8″, 1/2″, or 3/4″) that enables quick socket changes while maintaining precise torque transmission. The drive mechanism transfers rotational force through a square tang that engages corresponding recesses in socket tools, creating a positive mechanical lock under load.
Ratchet Wrench Mechanical Design
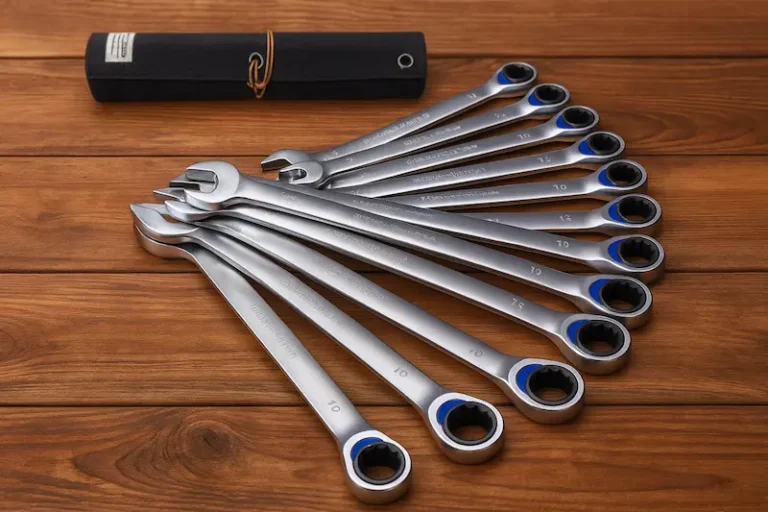
A ratchet wrench integrates the ratcheting mechanism directly into a fixed-size wrench head, eliminating the modular socket interface. The internal pawl and tooth system allows continuous rotation in the working direction while freewheeling during the return stroke, enabling operation in confined spaces with minimal handle swing.
Torque Transmission Analysis
Socket wrenches achieve superior torque transmission efficiency through their direct drive interface, typically maintaining 95-98% efficiency from handle to fastener. The positive engagement of square drive systems eliminates backlash and provides immediate torque response, critical for precision applications requiring specific torque values.
Ratchet Socket Wrench Hybrid Systems
Modern tool engineering has produced hybrid designs that combine socket modularity with integrated ratcheting mechanisms. These ratchet socket wrench tools provide the versatility of socket systems with the operational efficiency of ratcheting action, though they typically sacrifice some torque capacity for the added complexity.
Engineering Trade-offs
Each system involves specific engineering compromises. Socket wrenches prioritize maximum torque transmission and modular flexibility at the cost of operational efficiency in repetitive tasks. Ratchet wrenches optimize operational speed and ergonomics while accepting limitations in maximum torque capacity and size flexibility.
Check the Complete Guide to Types of Ratcheting Wrenches: Everything You Need to Know in 2025
Technical Specifications: Socket Wrench vs Ratchet Wrench Performance
Quantitative performance analysis reveals significant differences in the mechanical capabilities and operational characteristics of socket versus ratchet wrench systems. These specifications directly impact tool selection for specific applications and operational requirements.
Drive Size Standards and Torque Capacity: Socket wrench systems utilize standardized drive sizes with corresponding torque ratings. 1/4″ drives typically handle 15-50 ft-lbs, 3/8″ drives manage 30-150 ft-lbs, 1/2″ drives accommodate 75-400 ft-lbs, and 3/4″ drives support 200-1000+ ft-lbs. These ratings reflect the mechanical limits of the drive interface under static loading conditions.
Ratchet Wrench Torque Limitations: Fixed-head ratchet wrenches generally provide lower maximum torque capacity compared to equivalent-sized socket systems. The ratcheting mechanism introduces stress concentrations and mechanical complexity that typically limits torque capacity to 60-80% of comparable socket wrench systems. Professional-grade ratcheting wrenches often specify maximum torque limits to prevent mechanism damage.
Angular Precision and Operating Requirements: Socket wrenches require complete 360-degree rotation for operation, demanding full access around the fastener. Ratchet wrenches operate with minimal angular displacement—typically 5-15 degrees depending on tooth count—enabling operation in severely restricted spaces where socket wrenches cannot function.
Material Engineering and Durability: Socket wrench systems benefit from optimized material selection for each component. Drive handles utilize high-strength steel alloys optimized for torque transmission, while sockets employ specialized tool steels heat-treated for wear resistance and impact strength. This material optimization enables extended service life under demanding conditions.
Ratcheting Mechanism Complexity: The internal ratcheting mechanism requires precise manufacturing tolerances and specialized materials to maintain reliability. Premium ratchet wrenches feature hardened steel pawls, precision-ground teeth, and calibrated spring systems that must function reliably through millions of operating cycles while maintaining consistent engagement.
Dimensional Analysis and Space Requirements: Socket wrench systems typically require 25-40% more space than equivalent ratchet wrenches due to the socket extension beyond the drive head. This dimensional difference becomes critical in confined applications where every millimeter of clearance matters, such as engine compartments or industrial equipment maintenance.
How to Use a Ratchet Wrench: Complete Step-by-Step Guide
When to Use Socket Wrench vs Ratchet Wrench?
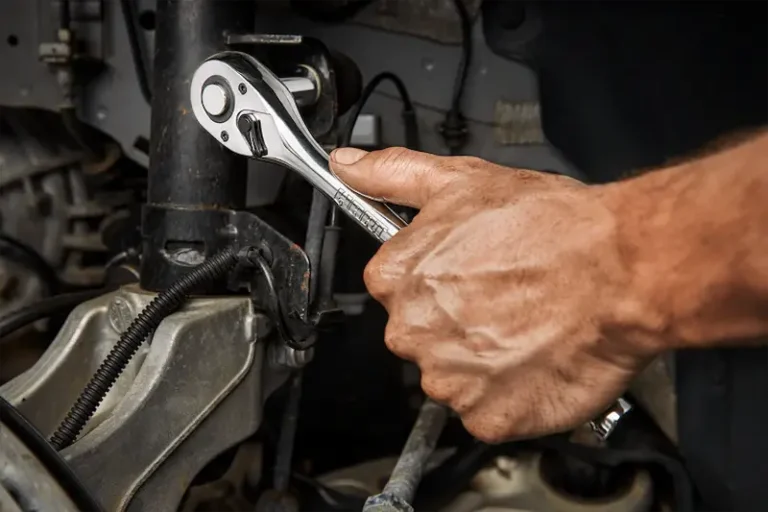
Engineering analysis of application requirements provides clear guidance for optimal tool selection based on specific operational parameters and performance requirements.
High-Torque Applications: Socket wrench systems excel in applications requiring maximum torque transmission, particularly in heavy industrial maintenance, construction equipment service, and large fastener applications. The direct drive interface and robust construction enable torque values exceeding 1000 ft-lbs when properly sized, making them essential for structural bolting and heavy machinery maintenance.
Precision Torque Control: Critical applications requiring precise torque specification benefit from socket wrench systems’ superior torque transmission characteristics. Aerospace assembly, engine rebuilding, and precision manufacturing applications rely on the consistent, backlash-free torque delivery that socket systems provide, enabling accurate torque wrench calibration and repeatability.
Repetitive Operation Efficiency: Ratchet wrench systems demonstrate clear advantages in applications involving numerous fasteners of similar size. Assembly line work, electrical panel installation, and maintenance tasks with repetitive bolt patterns benefit from the continuous operation capability that eliminates constant repositioning and reduces operator fatigue.
Find the Best Open End Ratchet Wrench Sets for 2025
Space-Constrained Environments: Confined space applications strongly favor ratchet wrench systems due to their minimal angular operating requirements. Automotive engine work, aircraft maintenance in wing areas, and industrial equipment service in tight quarters often require the 5-15 degree operating capability that only ratcheting mechanisms provide.
Mixed Fastener Size Applications: Socket wrench set configurations excel when applications involve multiple fastener sizes within a single project. The modular socket interface enables rapid size changes while maintaining consistent handle feel and torque characteristics, improving overall work efficiency compared to multiple fixed-size ratcheting wrenches.
Long-Duration Operations: Extended work sessions favor ratchet wrench systems for their ergonomic advantages and reduced physical stress. The continuous motion capability reduces hand and wrist fatigue compared to the repetitive repositioning required with socket wrenches, particularly important in professional environments where productivity depends on sustained performance.
Mechanical Efficiency: Socket vs Ratchet Wrench Performance Metrics
Quantitative efficiency analysis reveals significant performance differences between socket and ratchet wrench systems under various operating conditions and application requirements.
Time-Motion Study Results: Industrial engineering studies demonstrate that ratchet wrench systems reduce fastening time by 35-60% compared to socket wrenches in applications involving multiple turns per fastener. The continuous operation capability eliminates repositioning delays that accumulate significantly in repetitive tasks.
Torque Transfer Efficiency: Socket wrench systems achieve superior torque transfer efficiency, typically maintaining 95-98% of applied handle torque at the fastener interface. The positive mechanical engagement of square drive systems minimizes energy loss and provides immediate torque response essential for precision applications.
Operator Fatigue Analysis: Ergonomic studies indicate that ratcheting wrench systems reduce operator fatigue by approximately 25-40% during extended work sessions. The continuous motion capability eliminates the repetitive gripping and repositioning actions that contribute to hand and forearm fatigue in socket wrench operation.
Precision and Repeatability: Socket wrench systems demonstrate superior precision and repeatability in torque application, with typical variations of ±2-3% compared to ±5-8% for ratcheting systems. This precision advantage stems from the elimination of backlash and mechanical play inherent in ratcheting mechanisms.
Angular Efficiency Calculations: Ratchet wrench systems operate effectively with 5-15 degrees of handle swing, while socket wrenches require 60-180 degrees depending on fastener accessibility. This angular efficiency translates to 4-12 times fewer hand movements in space-restricted applications, dramatically improving productivity.
Load Distribution Analysis: The integrated design of ratchet wrenches distributes operational stresses across the entire tool body, while socket systems concentrate stress at the drive interface. This difference affects long-term durability and failure modes, with socket systems typically failing at drive interfaces while ratchet wrenches experience more gradual mechanism wear.
How Does a Ratchet Wrench Work? Complete Explained
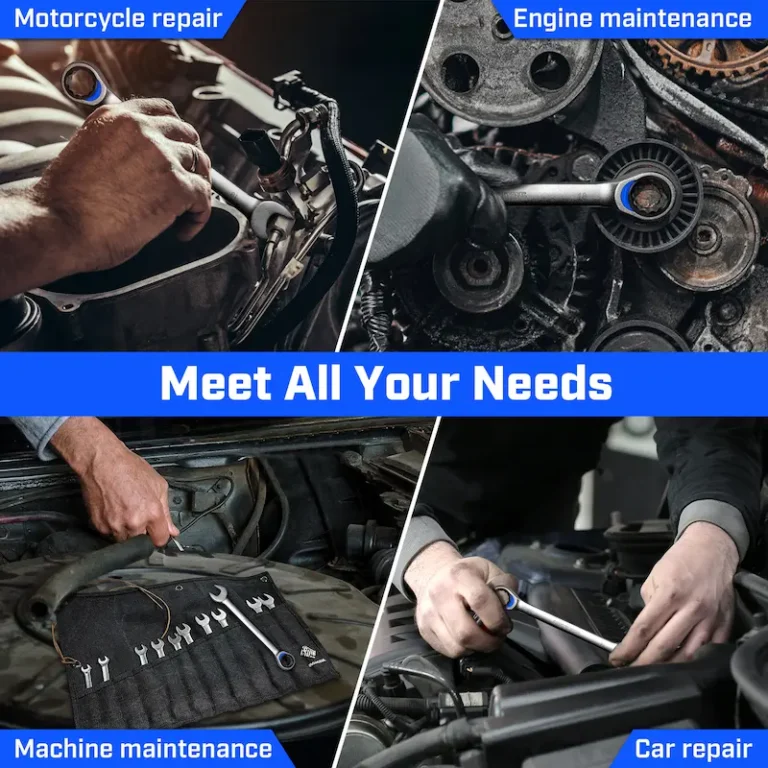
Tool System Compatibility: Socket and Ratchet Integration
Modern tool system design emphasizes modularity and cross-compatibility to maximize utility while minimizing inventory requirements and training complexity.
Standardization Benefits: Socket wrench systems benefit from decades of standardization efforts, with drive sizes, socket dimensions, and interface specifications governed by ANSI, DIN, and ISO standards. This standardization enables cross-brand compatibility and reduces inventory complexity in professional environments.
Modular System Advantages: The modular architecture of socket systems enables extensive customization through extensions, universal joints, adapters, and specialized sockets. This flexibility allows a single drive handle to address hundreds of different fastener configurations, maximizing return on tool investment.
Ratchet and Socket Set Integration: Modern tool collections often combine socket wrench systems with ratcheting drives, creating ratchet and socket set configurations that provide both modular flexibility and operational efficiency. These hybrid systems typically include both fixed-handle drives and ratcheting drives within comprehensive tool sets.
Cross-Platform Compatibility: Professional tool systems increasingly emphasize cross-platform compatibility, where socket sets work seamlessly with both traditional handles and ratcheting drives. This approach maximizes tool utility while providing operational flexibility for diverse applications.
Investment Optimization: The modular nature of socket systems enables incremental investment strategies where users can expand capability by adding specific sockets or accessories rather than purchasing complete new tool sets. This economic advantage becomes particularly significant in professional environments with diverse application requirements.
Quality Standardization: Professional-grade tool systems maintain consistent quality and performance characteristics across all components, ensuring that mixing brands or adding aftermarket components doesn’t compromise system performance or reliability.
Manufacturing Quality: Durability Comparison of Socket vs Ratchet Tools
Manufacturing quality directly impacts tool performance, longevity, and total cost of ownership in professional applications. Understanding quality differences guides appropriate tool selection and investment decisions.
Material Engineering Specifications: Premium socket wrenches utilize chrome vanadium steel or chrome molybdenum steel alloys with Rockwell hardness ratings of 38-45 HRC for optimal strength and toughness balance. Socket manufacturing employs drop-forging processes that align grain structure for maximum strength and impact resistance.
Ratcheting Mechanism Manufacturing: Quality ratchet wrench production requires precision machining of pawl and tooth interfaces to tolerances of ±0.001 inches or better. The internal mechanism typically uses hardened tool steel for pawls (58-62 HRC) and slightly softer steel for teeth (52-56 HRC) to optimize wear characteristics and prevent chipping.
Surface Treatment Technologies: Professional-grade tools employ multiple surface treatment processes including phosphate conversion coatings, chrome plating, and specialized corrosion-resistant finishes. These treatments provide corrosion protection while maintaining dimensional accuracy and surface finish requirements.
Quality Control Standards: Manufacturing quality control for professional tools includes 100% functional testing of ratcheting mechanisms, torque testing of drive interfaces, and dimensional verification of critical features. Premium manufacturers typically provide certificates of compliance with relevant standards and specifications.
Failure Mode Analysis: Socket systems typically fail through drive interface wear or socket cracking under overload conditions. Ratchet wrenches more commonly experience mechanism wear, pawl breakage, or spring fatigue. Understanding these failure modes enables appropriate maintenance strategies and replacement planning.
Service Life Expectations: Quality socket wrench systems in professional use typically provide 10-20 years of reliable service with proper maintenance. Ratcheting mechanisms generally require more frequent service or replacement, with typical professional service lives of 5-15 years depending on usage intensity and maintenance quality.
Understand what is a ratcheting wrench
Cost-Benefit Analysis: Socket Wrench vs Ratchet Wrench Investment
Total cost of ownership analysis provides essential data for tool investment decisions in professional environments where tool costs directly impact operational profitability.
Initial Investment Comparison: Comprehensive socket wrench sets typically require higher initial investment ($200-800 for professional sets) compared to equivalent ratcheting wrench sets ($150-600). However, the modular nature of socket systems often provides broader capability coverage per dollar invested.
Productivity Impact Quantification: Time-motion studies in automotive service environments demonstrate 20-45% productivity improvements when using appropriate ratcheting tools for repetitive fastening tasks. This productivity improvement translates to measurable labor cost reductions that often justify premium tool investment within 6-12 months.
Maintenance and Replacement Costs: Socket systems generally require lower long-term maintenance costs due to their simpler mechanical design and replaceable component architecture. Individual socket replacement costs $5-25 compared to complete ratchet wrench replacement costs of $30-150 when mechanisms fail.
Operational Efficiency Calculations: Professional mechanics report 15-30% time savings when using ratcheting tools for appropriate applications. In commercial environments billing $100-150/hour, these efficiency gains generate substantial return on investment through increased billable hour capacity.
Total Cost of Ownership (TCO): Five-year TCO analysis for professional tool investments typically favors socket systems for diverse applications and ratcheting systems for specialized repetitive work. The optimal approach often involves strategic combinations that maximize overall system efficiency.
Return on Investment (ROI): Professional-grade tool investments typically achieve positive ROI within 12-24 months through improved productivity, reduced operator fatigue, and decreased fastener damage. Premium tools often provide superior ROI through extended service life and consistent performance characteristics.
Professional Case Studies: Socket vs Ratchet Wrench in Real Applications
Real-world application analysis provides practical insights into tool performance under actual working conditions and operational requirements.
Aerospace Manufacturing Case Study: Boeing assembly lines utilize socket wrench systems for critical structural bolting operations requiring precise torque specifications and traceability. The consistent torque transmission characteristics and calibration capabilities of socket systems enable compliance with stringent quality requirements while maintaining production efficiency.
Automotive Production Line Analysis: Toyota assembly plants employ ratcheting wrench systems for body panel fastening and interior component installation where speed and operator comfort drive tool selection. The continuous operation capability reduces cycle time while minimizing operator fatigue in high-volume production environments.
Heavy Industrial Maintenance Application: Caterpillar service centers report 40% time savings using appropriate socket wrench systems for hydraulic component service and engine overhaul operations. The high torque capacity and precise control enable efficient service of large fasteners while maintaining quality standards.
Electronics Manufacturing Environment: Apple contract manufacturers utilize precision ratcheting tools for device assembly operations where small fasteners and confined spaces require specialized tool characteristics. The minimal angular requirements and precise control enable high-quality assembly in space-constrained applications.
Marine Maintenance Operations: US Navy maintenance protocols specify socket wrench systems for critical engine and propulsion system service due to their reliability under harsh environmental conditions and ability to handle high-torque applications essential for operational readiness.
How to Use a Ratchet Wrench: Complete Step-by-Step Guide
Precision Medical Device Assembly: Medical device manufacturers rely on precision ratcheting tools for implant assembly and surgical instrument manufacturing where contamination control and precise torque application are critical for patient safety and regulatory compliance.
How to Choose Between Socket Wrench and Ratchet Wrench?
Systematic decision-making frameworks enable optimal tool selection based on quantifiable criteria and specific application requirements rather than subjective preferences or traditional practices.
Application Requirements Assessment: Primary considerations include maximum torque requirements, space constraints, fastener size variety, precision requirements, and operational volume. These factors directly influence which tool system provides optimal performance for specific applications.
Operational Environment Analysis: Environmental factors including contamination levels, temperature extremes, accessibility constraints, and maintenance support availability significantly impact tool selection and long-term performance characteristics.
Economic Impact Evaluation: Tool investment decisions should consider initial costs, productivity improvements, maintenance requirements, operator training needs, and total cost of ownership over the expected service life of the tools.
Quality and Precision Requirements: Applications requiring specific torque values, repeatability, or quality documentation typically favor socket systems, while speed-critical applications with standard fasteners often benefit from ratcheting mechanisms.
System Integration Considerations: Tool selection should align with existing equipment, training programs, and maintenance capabilities to maximize overall system efficiency and minimize operational disruption during implementation.
Future Needs Planning: Consideration of anticipated application changes, volume growth, and technology evolution ensures tool investments remain valuable throughout their service life and support business development objectives.
Conclusion and Technical Recommendations
The socket wrench versus ratchet wrench decision fundamentally depends on specific application requirements, operational constraints, and performance priorities rather than universal superiority of either system.
Socket Wrench Systems Excel: In applications requiring maximum torque transmission, precise torque control, diverse fastener sizes, and maximum durability. These tools provide superior performance for heavy-duty applications, precision assembly, and situations where torque specifications are critical for safety or quality.
Ratchet Wrench Systems Optimize: Operational efficiency in repetitive tasks, confined space applications, and situations where operator comfort and speed drive productivity. These tools deliver clear advantages in assembly operations, maintenance tasks, and applications where access limitations prevent effective socket wrench use.
Integrated Approaches: Modern professional environments increasingly employ strategic combinations of both systems, selecting specific tools based on application requirements rather than committing to single-system approaches. This strategy maximizes overall efficiency while ensuring optimal tool performance across diverse applications.
Investment Strategy: Professional tool investment should prioritize quality over initial cost, considering the long-term impact of tool performance on productivity, quality, and operational costs. Premium tools typically provide superior return on investment through improved performance and extended service life.
Technology Evolution: Continuing advances in materials, manufacturing, and digital integration will enhance both socket and ratcheting systems, making tool selection increasingly application-specific rather than technology-limited. Future developments will likely focus on improved ergonomics, enhanced durability, and integrated smart capabilities that provide new levels of performance and control.