How does a ratchet wrench work to create this revolutionary advantage that transforms tedious bolt-turning into smooth, efficient motion? This seemingly simple tool harbors one of mechanical engineering’s most elegant solutions, combining spring-loaded precision with directional intelligence to solve a problem that plagued workers for centuries.
Understanding how does ratchet wrench work opens a window into ingenious mechanical design where every component serves a critical purpose. From the precisely machined teeth to the spring-loaded pawl, each element contributes to a mechanism that allows continuous rotation in one direction while preventing reverse motion—a breakthrough that revolutionized everything from automotive repair to aerospace assembly.
Ratchet Wrench Components: Understanding the Basic Structure
A ratchet wrench typically consists of several key components working in precise mechanical harmony. The handle provides leverage, often featuring an ergonomic grip designed to minimize fatigue during extended use. Modern handles may incorporate rubberized or textured materials to maintain a secure grip even under exposure to oils, grease, or moisture commonly encountered in mechanical tasks.
The ratchet head is the core of the tool, containing multiple precision-engineered components, including the ratchet gear with finely machined teeth, a spring-loaded pawl that engages these teeth, and a directional control mechanism. These components are enclosed within a robust housing designed to withstand high torque and frequent stress, manufactured from heat-treated hardened steel, often machined to tolerances within ±0.001 inches for professional-grade accuracy.
The drive square provides the critical interface between the wrench and various sockets or attachments, typically sized at 1/4″, 3/8″, 1/2″, or 3/4″, with larger or smaller specialized sizes occasionally available (such as 1″ for heavy-duty applications). This square drive typically includes a spring-loaded ball bearing retention system for quick and secure socket attachment and removal.
The external appearance of a ratchet wrench often conceals internal complexity. A small lever or rotary collar, known as the directional switch, controls the engagement of the pawl, selecting clockwise, counterclockwise, or sometimes a locked position which converts the ratchet into a fixed wrench. Alternative designs such as push-through switches are also common in some specialty ratchet wrenches.
High-quality ratchets usually feature tooth counts ranging from 72 to over 120 teeth, with higher tooth counts offering smaller swing angles beneficial in confined spaces—commonly 5° for 72 teeth, 4° for 90 teeth, or 3° for 120 teeth. Professional users often pay close attention to these angles, as they significantly impact usability in tight working conditions.
How Does Ratchet Work: The Ingenious Pawl Mechanism Explained
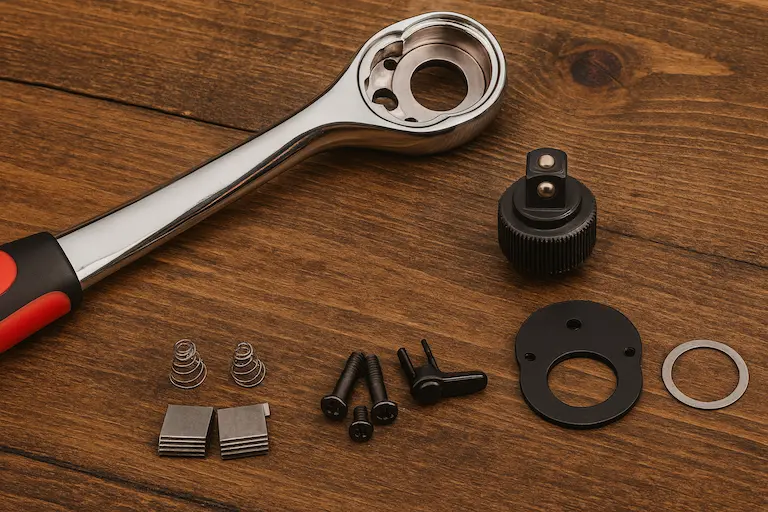
The ratchet mechanism is based on a clever yet simple mechanical principle, achieving unidirectional transmission of rotational motion and preventing reverse rotation through the asymmetric mechanical engagement between the pawl and the ratchet gear. Its core component—the pawl—is a spring-driven lever that engages with the precisely machined teeth on the ratchet gear, forming what is known in engineering as a one-way clutch.
When the user applies rotational force in the working direction, the inclined surface of the pawl precisely contacts the inclined surface of the ratchet gear teeth and locks tightly, efficiently transmitting the input torque to the output square drive. In this process, the geometric parameters between the pawl and gear teeth (pawl angle, tooth pitch) work in close coordination with spring tension to ensure stable engagement of the ratchet gear under load conditions, preventing slippage, while also allowing smooth disengagement during reverse rotation.
During reverse rotation, the pawl contacts the steep surface of the gear teeth and slides along the tooth surface, producing the characteristic clicking sound. The spring quickly returns the pawl to its initial position, completing the ratcheting cycle and preparing for the next engagement. This cycle may repeat dozens of times per rotation, with each click representing a precision mechanical control cycle.
The number of teeth determines the precision and operable angle of the ratchet. Common ratchet tooth counts include 72 teeth (5°), 90 teeth (4°), or even 120 teeth (3°). The more teeth, the finer the movement per step, the smaller the required operating space, but the manufacturing cost and material requirements also increase accordingly.
Springs are critical in ratchet mechanisms. If spring tension is too low, the pawl may bounce under heavy loads; if too high, it reduces return speed and accelerates wear. High-end ratchets use special alloy steel springs that undergo heat treatment and surface hardening, maintaining stable elasticity even after millions of cycles.
Additionally, temperature changes significantly affect ratchet performance. At low temperatures, lubricants become viscous, causing springs to respond slowly; at high temperatures, thermal expansion can occur, leading to changes in meshing clearance. High-quality ratchets typically use special lubricants and heat treatment technologies to ensure consistent performance within the temperature ranges commonly encountered in professional applications.
Finally, material selection and surface treatment are critical factors in determining tool durability. Ratchet wheels and pawls are typically made from heat-treated hardened steel, or undergo additional processes such as nitriding, electroplating, or coating to enhance hardness and wear resistance, thereby extending tool lifespan.
Find The Best Ratcheting Wrench Sets For You From Ironcube
How Ratchet Wrench Works In Action
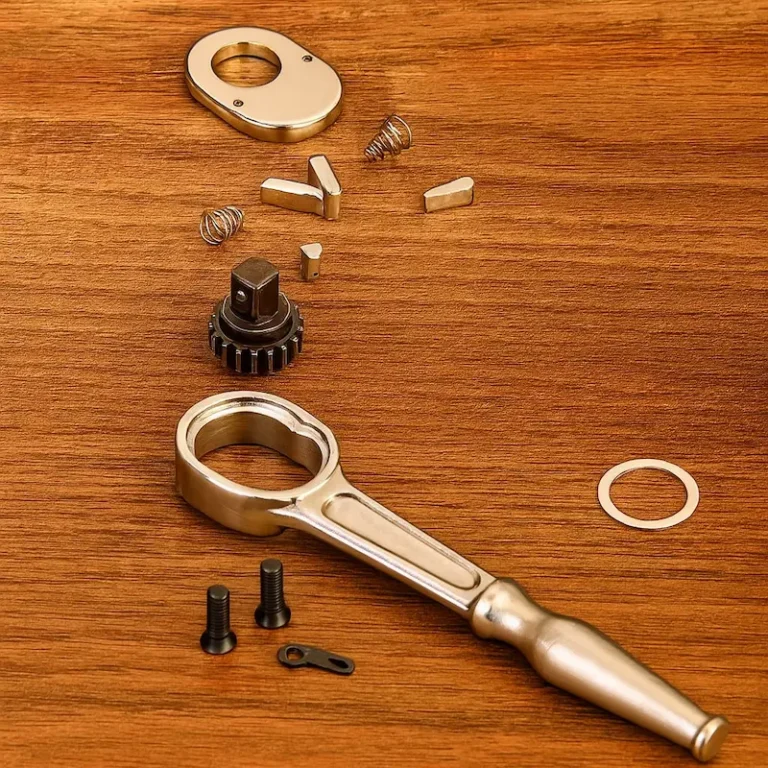
To gain a deeper understanding of the working principle of a ratchet wrench, we can break down its operational cycle into four steps for detailed analysis:
Initial Engagement
First, securely attach the socket to the fastener. When the handle is subjected to an initial rotational force, the pawl engages with the ratchet gear teeth under spring force, typically engaging multiple tooth surfaces simultaneously to distribute the load. Kamm, L.J. notes in *Designing Cost-efficient Mechanisms* (McGraw-Hill Professional): The use of multiple-tooth engagement significantly reduces the load per tooth, enhancing durability and reliability.”
Torque Transmission
The torque multiplication effect of a ratchet wrench stems from the lever principle provided by the handle length. For example, a 10-inch ratchet handle can achieve approximately an 8:1 mechanical advantage. This means that applying moderate force can easily generate significant torque: applying 15 pounds (approximately 6.8 kilograms) of force at the handle end can produce over 100 inch-pounds (approximately 11 Newton-meters) of torque. Spotts, M.F. and Shoup, T.E. describe in *Design of Machine Elements* (8th ed., Pearson Education): “A 10-inch handle provides roughly an 8:1 mechanical advantage, meaning moderate hand force can generate substantial torque, such as applying 20 pounds of force to achieve approximately 200 inch-pounds of torque.”
Return Stroke
When the wrist is rotated to the operational limit, the operator must reverse the handle direction. The ratchet pawl disengages from the meshed position and smoothly slides over the back of the gear, producing a distinct clicking sound. Each clicking sound indicates that the ratchet has moved past one tooth. The frequency of the clicking sound depends on the number of teeth on the ratchet wheel; the more teeth, the more frequent the clicking sound. For example, a 72-tooth ratchet wheel produces a clicking sound every 5 degrees of rotation, while a 120-tooth ratchet wheel does so every 3 degrees, allowing operation in narrower spaces. Collins, J.A. and Busby, H.R. explicitly state in *Mechanical Design of Machine Elements and Machines* (2nd ed., Wiley): “The clicking sound frequency is directly proportional to tooth count; higher tooth counts yield more frequent clicks per degree of rotation. For example, a 72-tooth ratchet produces a click every 5°, while a 120-tooth ratchet clicks every 3°.”
Re-engagement
After completing the rotation, the pawl quickly re-engages into position, ready for the next torque application. This process automatically repeats in a cycle, enabling the ratchet wrench to operate efficiently in confined spaces. Budynas, R.G., and Nisbett, J.K., in *Shigley’s Mechanical Engineering Design* (11th ed., McGraw-Hill Education), explain: “Rapid re-engagement of the pawl is crucial for efficient ratcheting action, particularly beneficial in constrained spaces.”
The most notable advantage of ratchet wrenches is their ability to work effectively in confined spaces. High-end ratchet wrenches on the market typically have between 72 and 120 teeth, or even more, with a minimum operating angle as low as 3°, making them particularly suitable for maintenance work in complex spaces such as engine compartments and the interiors of mechanical equipment. Norton, R.L. emphasizes in *Machine Design: An Integrated Approach* (4th ed., Pearson Education): “High-quality ratchets typically offer minimal operational angles ranging from 3° to 5°, significantly outperforming traditional fixed wrenches, especially in engine bays and complex machinery.”
Additionally, professional technicians often assess tool quality based on the feel of the ratchet wrench (such as smooth gear engagement, consistent clicking sounds, and precise directional control). High-quality ratchets maintain precise engagement and clear tactile feedback even after millions of operations, while lower-quality ratchets quickly exhibit loosening, increased gear play, or inaccurate directional control. Childs, P.R.N. notes in *Mechanical Design* (2nd ed., Butterworth-Heinemann): “Premium ratchets maintain precise engagement and clear tactile feedback even after millions of cycles, whereas inferior models quickly develop looseness, increased backlash, and unreliable direction control.”
2025 The Best Multi Ratcheting Screwdriver Set Guide
Types of Ratchet Mechanisms in Different Wrench Designs
Modern ratchet wrenches employ a variety of mechanical designs tailored for different applications. Understanding the specific characteristics of each design helps professionals choose the appropriate tool for the job:
Fine-Tooth Ratchet Mechanisms (80-120 Teeth)
Fine-tooth ratchets feature closely spaced teeth, typically ranging from 80 to 120 or even higher. The increased tooth count significantly reduces the minimum swing angle (often between 3° and 5° per click), making them ideal for confined spaces and precision applications such as automotive engine compartments or intricate machinery assembly.
However, their smaller, more delicate teeth demand higher manufacturing precision and tighter tolerances, often within ±0.001 inches. Due to their delicate nature, fine-tooth mechanisms may be more vulnerable to damage under extreme torque loads or improper usage.
Coarse-Tooth Ratchet Mechanisms (24-36 Teeth)
Coarse-tooth ratchets generally incorporate fewer, larger teeth (24-36 teeth), which results in a greater swing arc (usually around 10°–15° per click). Although this limits their use in tight spaces, the larger teeth significantly enhance durability, allowing these tools to withstand higher torque loads and rough handling.
These robust mechanisms are favored in heavy-duty industrial environments and professional automotive maintenance, where reliability, strength, and resistance to extreme forces are prioritized over minimal swing requirements.
Dual-Pawl Ratchet Mechanisms
Some premium ratchet designs use dual pawls positioned approximately 180 degrees apart around the ratchet gear. This configuration distributes torque more evenly across multiple points of contact, reducing individual component stress and enhancing operational smoothness. The dual-pawl setup also provides redundancy, increasing reliability, and extending the overall lifespan of the tool, particularly under repetitive, heavy-duty use.
However, dual-pawl mechanisms demand precise manufacturing and assembly, resulting in increased complexity and production costs. Consequently, these designs typically appear in high-end professional or industrial-grade tools.
Discover what is a ratcheting wrench
Quick-Release Ratchet Mechanisms
Quick-release ratchet designs incorporate mechanisms that enable rapid, tool-free socket or attachment changes. Common designs include:
Push-button release: Pressing a button on the ratchet head depresses an internal retention ball, allowing easy socket removal.
Pull-release collar: A sliding collar mechanism around the ratchet head releases sockets when pulled.
While these designs greatly enhance convenience and efficiency, they must reliably secure sockets under high torque conditions—presenting a significant engineering challenge. Quality quick-release mechanisms carefully balance ease of use with secure retention through precision engineering and durable materials.
Sealed Ratchet Mechanisms
Sealed ratchet designs feature enclosed mechanisms to protect internal components from environmental contaminants such as dust, dirt, moisture, and saltwater. Typically, these mechanisms use specialized O-ring seals, gaskets, and precisely fitted covers. The sealing helps maintain consistent lubrication, essential for smooth operation over extended periods, especially under adverse conditions.
Due to the sealed nature, specialized lubricants with stable viscosity across varying temperature ranges—such as synthetic or silicone-based greases—are employed to ensure reliable performance. These sealed designs are particularly valuable in marine, aerospace, off-road, and military applications, where environmental protection directly impacts tool longevity and operational reliability.
Types of Ratchet Mechanisms in Different Wrench Designs
Modern ratchet wrenches incorporate various mechanical structural designs to accommodate different application scenarios and performance requirements. The following classifications outline the characteristics and suitable applications of various ratchet designs:
Fine-Tooth Ratchet (80-120 teeth)
Fine-tooth ratchets typically have 80 to 120 teeth or more, with extremely small tooth spacing. The angle of each step (working angle) is usually only 3° to 5°, making them ideal for use in narrow or precision mechanical environments, such as automotive engine maintenance and precision equipment servicing.
However, due to the small size of the gear teeth, manufacturing precision requirements are extremely high (tolerances are generally within ±0.025mm). The gears are typically made from heat-treated hardened steel to reduce wear and damage risks. However, under high loads or improper operation, they are relatively more prone to damage, so they are typically used in medium to low torque applications.
Coarse-Tooth Ratchet (24-36 teeth)
Coarse-tooth ratchets typically have only 24-36 teeth, with larger tooth spacing and a single-step action angle of approximately 10° to 15°. While this design offers limited operational flexibility in space-constrained environments, the larger gear teeth significantly enhance ratchet strength and durability, enabling higher torque transmission capabilities (e.g., exceeding 200 Nm).
Coarse-tooth ratchets are commonly used in professional automotive repair and heavy industrial assembly applications due to their ability to maintain long-term reliability and high impact resistance and wear resistance under harsh conditions.
Dual-Pawl Mechanism
Some high-end ratchets feature two pawls symmetrically mounted 180 degrees apart, forming a dual engagement with the ratchet gear. This design distributes the load more evenly when the ratchet is under force, significantly reducing the load on a single pawl and improving the overall smoothness and service life of the tool.
The dual-pawl structure is commonly used in environments requiring frequent use, high loads, and long-term operation, such as industrial production lines, aircraft maintenance, and automotive assembly. However, this structure demands extremely high production precision and assembly工艺 requirements, resulting in increased costs.
Quick-Release Mechanism
The quick-release ratchet structure allows users to instantly replace the socket without additional tools, improving operational efficiency. Common quick-release mechanisms include:
Button-type quick release: Pressing the button on the ratchet head releases the socket instantly via an internal steel ball or locking pin.
Ring-type quick release: Pushing the ring-shaped sleeve releases the socket.
Quick-release designs must strike a precise balance between convenience and reliability to ensure that sockets remain securely fixed under high torque conditions and do not accidentally detach. Achieving this requires stringent material selection (typically high-strength spring steel) and mechanism precision (tolerance within ±0.02mm).
Sealed Ratchet Mechanism
The sealed ratchet design completely encloses the internal meshing mechanism with O-rings, rubber seals, or special sealing gaskets to prevent dust, moisture, salt fog, and other external contaminants from entering. This structure is particularly suitable for applications with strict environmental protection requirements, such as:
Aerospace equipment maintenance
Marine engineering and ship maintenance
Military or outdoor tools for extreme environments
Due to the fully enclosed internal structure, sealed ratchets require specialized lubricants (typically synthetic or silicone-based grease) to provide continuous and stable lubrication protection across a wide temperature range (-30°C to 120°C), ensuring smooth and reliable tool operation over the long term.
Sealed ratchets have higher production costs and strict requirements for dustproof and waterproof processing during assembly, so they are generally used in high-end professional-grade tools.
Material and Process Supplementary Notes:
Various ratchet gears and pawls are typically made of alloy steel, which undergoes heat treatment (such as quenching and tempering) to enhance wear resistance and strength.
Surface treatments include chrome plating, nitriding, or special coatings to enhance rust and corrosion resistance.
Who Invented the Ratchet Wrench?
The question of “who invented the ratchet wrench” reveals a story of mechanical innovation spanning hundreds of years. The ratchet, a clever one-way mechanism, can be traced back to the 16th century, when it was first used in winches and clock spring mechanisms. However, it was not until after the Industrial Revolution that ratchets were ingeniously incorporated into hand tools.
19th Century: The Dawn of Ratchet Tools
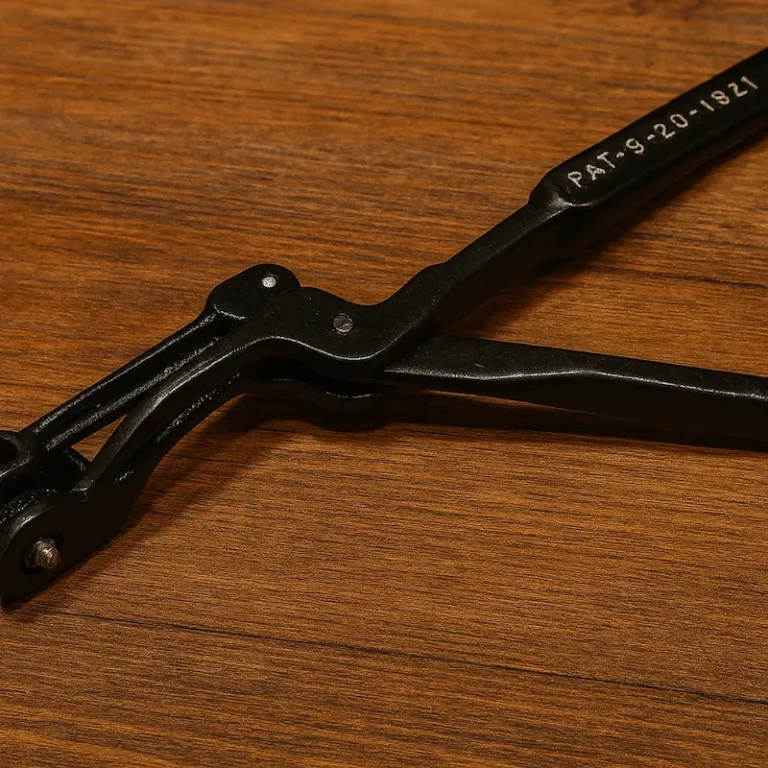
The prototype of the modern ratchet wrench emerged at the end of the 19th century. As the Industrial Revolution drove advancements in precision machining technology, the mass production of complex mechanical components became possible for the first time, and ratchet mechanisms began to transition from large-scale machinery into the realm of small, precision hand tools. Although no single inventor is explicitly recorded, many mechanics and manufacturers in the United States and Europe began experimenting with ratchet applications in wrenches during the late 19th century. For example, William J. Brady’s 1871 U.S. patent (US116424A) was the first to describe the concept of a ratchet mechanism in manual tools.
Early 20th Century: Commercialization of Ratchet Wrenches
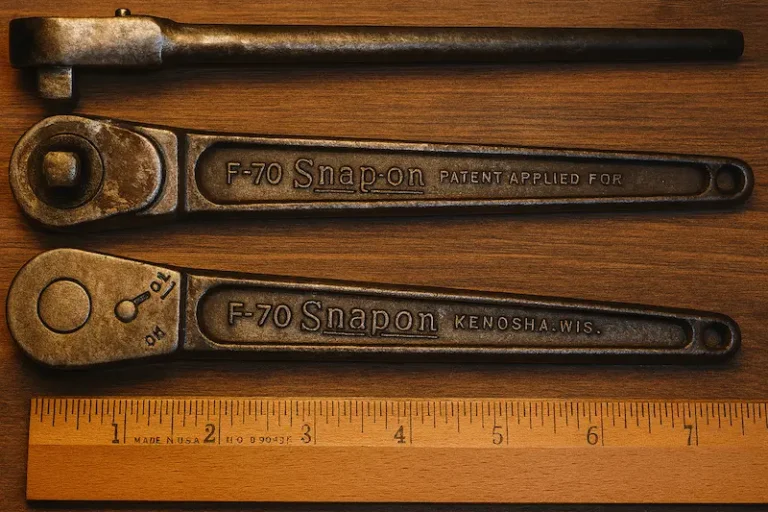
It was American tool manufacturers in the early 20th century who truly popularized and achieved commercial success with ratchet wrenches. The most notable was Snap-on, founded in 1921, whose inventor Joseph Johnson created the ratchet wrench with interchangeable sockets (Ratchet and interchangeable socket wrench). This innovation significantly enhanced the efficiency and convenience of mechanics’ work, revolutionizing the automotive repair industry. Additionally, companies like S-K Tools and Craftsman emerged during this period, further enhancing the strength, precision, and reliability of ratchet wrenches through improvements in steel quality, gear manufacturing techniques, and heat treatment processes.
Post-World War II Prosperity and Innovation (1940s–1960s)
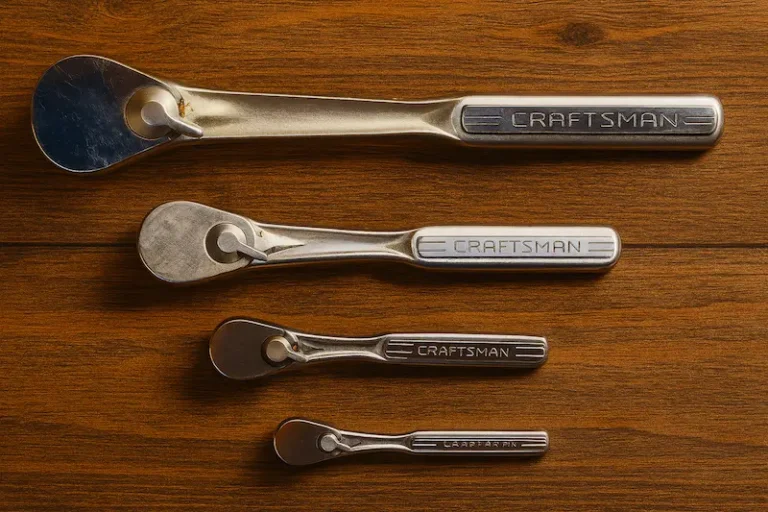
Following World War II, the global automobile ownership rate surged, leading to a sharp increase in demand for automotive maintenance and repair. This significantly drove the innovation of ratchet wrench technology:
In the 1950s, more refined gear designs (such as 40-60 teeth) emerged, significantly reducing the space required for operations.
In 1965, Stanley Works introduced the Quick-Release mechanism, enabling faster and more convenient socket changes, which was widely welcomed by technicians.
During the same period, tool manufacturers in the United States, Germany, and Japan launched precision ratchet tools, such as German Hazet and Japanese KTC (Kyoto Tool) companies, setting new global standards in precision machining, wear-resistant treatment, and ergonomic design.
Modern ratchet wrenches (1970s to present): A revolution in materials and design
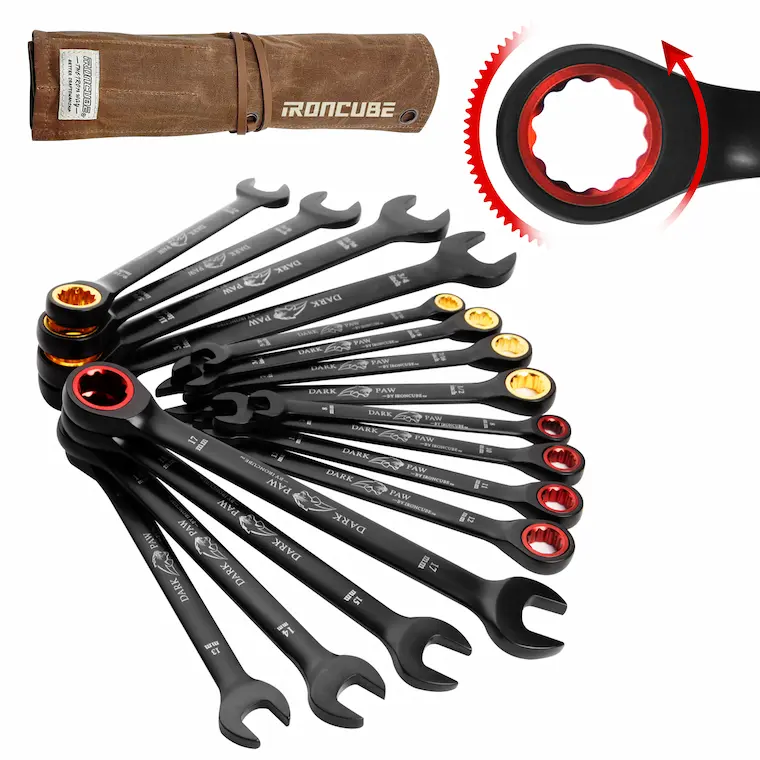
Since the late 20th century, ratchet wrench development has entered a new phase integrating materials science, precision manufacturing, and ergonomics:
In the 1980s, Snap-on and FACOM (a French tool brand) pioneered the dual-claw ratchet design, further enhancing tool durability and smoothness.
From the late 1990s to the 2000s, advancements in computer-aided design (CAD), computer numerical control (CNC) technology, and powder metallurgy processes enabled ratchet mechanism manufacturing tolerances to be refined to the micron level, significantly improving ratchet quality and performance stability.
At the beginning of the 21st century, numerous innovations emerged to address the needs of specialized industries, such as dustproof and waterproof sealing designs (suitable for aerospace, military, and marine applications), low-profile ultra-thin designs (suitable for automotive engine maintenance), and ergonomic handle designs (enhancing comfort during prolonged use).
Common Fault Analysis and Repair of Ratchet Mechanism
Ratchet mechanism failures often manifest as jumping, binding, or loss of directional control. Pawl wear is the most common problem and is usually caused by wear caused by long-term high-load use or contamination. A worn pawl may slip or fail to engage consistently under load, requiring replacement of the entire mechanism in most designs.
Spring failure affects engagement reliability and smooth return action. Contaminated springs may bind or break, while springs that have lost tension will not maintain proper pawl-to-tooth contact. Springs used in quality ratchets are designed to last millions of cycles, but even quality parts will eventually need to be replaced in high-use applications.
Tooth damage is often caused by shock loading or using the wrong tool. Impact damage can cause individual teeth to chip or deform, creating rough spots that affect smooth pawl operation. Once teeth are damaged, the entire ratchet head usually needs to be replaced, as repairs are generally not economical.
Directional control problems often stem from contamination or wear of control components in the switching mechanism. Dirt, grease, or metal particles can affect the proper operation of the switch, and worn components may not reliably hold position. Most of these problems can be avoided with regular cleaning and lubrication.
The correct method for cleaning a ratchet wrench involves disassembling the mechanism, cleaning it thoroughly with a suitable solvent, inspecting all parts, and reassembling with proper lubrication. However, many modern ratchet wrenches feature sealed mechanisms that require specialized tools and techniques for proper maintenance, making professional repair more practical than user maintenance.